Printing on silicone cups requires different techniques depending on the design, production scale, and durability required. In this guide, we will explore the five most popular methods: debossing/embossing, laser engraving, pad printing, heat transfer printing, and water transfer printing. Each technique offers unique benefits, allowing you to achieve different design goals.
Debossed or Embossed Logo on Silicone Cups
Debossing and embossing involve altering the physical surface of the silicone cup to create raised (embossed) or recessed (debossed) designs. These methods are perfect for creating a premium, tactile feel that doesn't rely on inks or paints, making the design durable and long-lasting.
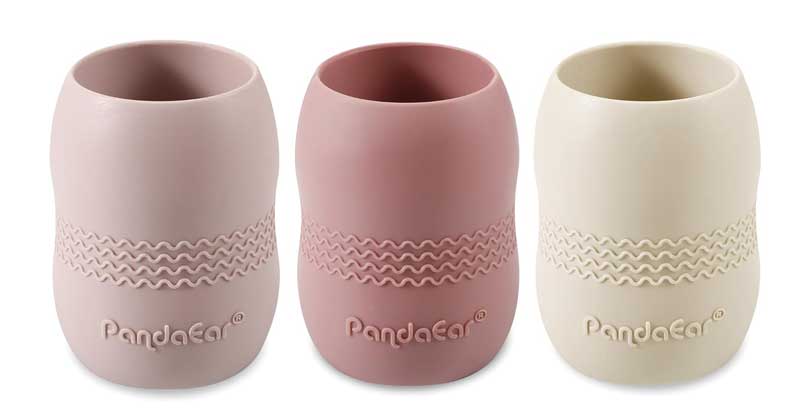
Step-by-Step Process
- Create the Mold: The first step is creating a mold or die with the desired logo or design. For debossing, the logo is etched into the mold, and for embossing, the design is raised.
- Heat the Mold: The silicone cup is placed into the mold, and heat and pressure are applied. This causes the silicone to conform to the mold, creating the desired debossed or embossed effect.
- Cool and Remove: Once the molding process is complete, the cup is cooled, and the mold is carefully removed, leaving behind the embossed or debossed logo.
Advantages:
- Durability: The design will not wear off over time, as it is part of the cup’s material.
- Premium Finish: Adds a tactile and sophisticated feel to the product.
Laser Engraving on Silicone Cups
Laser engraving involves using a high-powered laser to etch a design directly onto the surface of the silicone cup. This process is precise, allowing for intricate patterns, logos, or text to be engraved onto the silicone.
Step-by-Step Process
- Set Up the Laser Engraving Machine: Upload your design file to the laser engraving machine and adjust the settings based on the cup's material (silicone) and thickness.
- Clean the Cup: Ensure the silicone cup is clean and free from dust and oil to achieve the best results.
- Engrave the Design: The laser beam vaporizes the top layer of the silicone, leaving behind an engraved mark of the design. The depth and precision can be adjusted depending on the settings.
- Clean the Engraved Surface: After engraving, clean the cup to remove any residue or debris left by the laser.
Advantages:
- High Precision: Allows for detailed, intricate designs.
- Durability: The engraving is permanent and will not fade over time.
Pad Printing on Silicone Cups
Pad printing is a versatile method that transfers ink from an engraved plate onto a silicone cup using a silicone pad. It's ideal for printing detailed logos, text, or images, especially on curved or irregularly shaped surfaces.
Step-by-Step Process
- Prepare the Plate and Ink: Use a silicone-compatible ink and engrave the design onto a metal plate.
- Pick Up the Ink: The silicone pad presses onto the engraved plate, picking up the ink from the recessed design.
- Transfer the Design: The ink-covered pad is then pressed onto the silicone cup, transferring the design.
- Curing the Cup: After printing, the cup is placed in an oven or under UV light to cure the ink and ensure it adheres to the silicone.
Advantages:
- Ideal for Curved Surfaces: Works well on non-flat surfaces like cups.
- High Detail: Suitable for intricate designs and small logos.
Heat Transfer Printing on Silicone Cups
Heat transfer printing involves transferring a pre-printed design onto a silicone cup using heat and pressure. This method is great for multi-color and high-quality images.
Step-by-Step Process
- Print the Design: The design is printed on a transfer paper using special silicone ink.
- Position the Design: The transfer paper is placed on the silicone cup in the desired location.
- Heat Press: A heat press machine is used to apply heat and pressure to the cup, transferring the ink from the paper onto the silicone.
- Cure the Cup: Once the design is transferred, the cup is cured in an oven to ensure the ink fully adheres to the silicone surface.
Advantages:
- Vivid Colors: Capable of printing detailed, multi-colored designs.
- Smooth Finish: Provides a smooth, professional-looking print.
Water Transfer Printing on Silicone Cups
Water transfer printing, also known as hydrographics, allows for the application of intricate, full-color designs on silicone cups. This method is often used for patterns, such as camouflage or marble, which are difficult to achieve through traditional printing methods.
Step-by-Step Process
- Prepare the Film: Print the design on a water-soluble film.
- Activate the Film: Place the film on the surface of a water tank and spray an activator solution to dissolve the film, leaving the ink floating on the water.
- Dip the Silicone Cup: Submerge the silicone cup into the water, allowing the ink to wrap around the surface of the cup.
- Rinse and Cure: Once the design has transferred, rinse the cup to remove any excess film and cure it to ensure the ink bonds to the silicone.
Advantages:
- Full Surface Coverage: Perfect for designs that need to cover the entire surface of the cup.
- Complex Patterns: Ideal for detailed, multi-color patterns that are difficult to achieve with other methods.
Conclusion
When printing on silicone cups, choosing the right method depends on the design complexity, desired durability, and aesthetic goals. Debossing/embossing offers a premium, tactile finish, while laser engraving is excellent for precision and durability. For detailed logos and small designs, pad printing is ideal, while heat transfer printing is great for multi-colored, smooth finishes. If you're looking for all-over coverage or complex patterns, water transfer printing provides the best solution.
By understanding the benefits and processes of each method, manufacturers can select the optimal printing technique for their specific needs, ensuring high-quality results on every silicone cup.