Need custom silicone parts but confused by the cost? Unexpected expenses can wreck your budget. Understanding what drives the price helps you plan accurately and get the best value for your project.
The cost for a custom silicone production mold typically ranges from $1,500 to over $10,000. This price depends on the product's size, complexity, and required production volume. Simpler, smaller sample molds can be much cheaper, starting around a few hundred dollars.
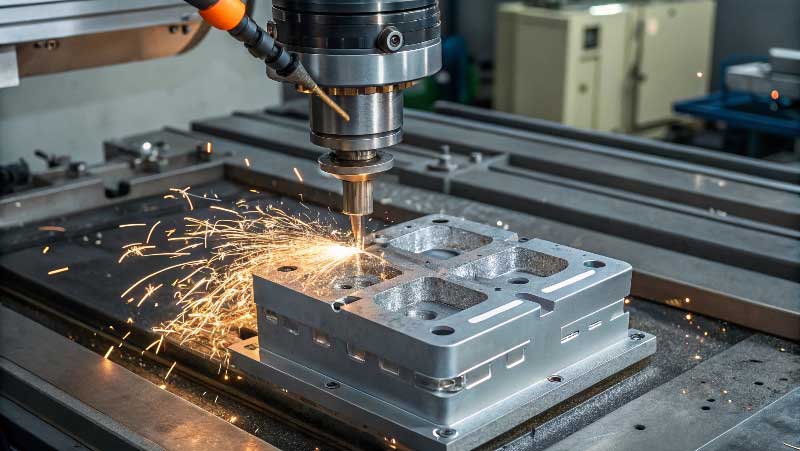
I'm Peter, and running a silicone factory has taught me that cost is the number one question on every client's mind. Procurement professionals like Alex need solid numbers for their budgets, not vague guesses. The price for a mold isn't just an arbitrary number; it's a result of very specific factors like steel quality, machine time, and design complexity. Let's break down the common questions I hear about cost so you can understand exactly what you are paying for and why it's a critical investment in your product's quality.
Is silicone casting expensive?
You want to create a few prototypes but fear the high startup costs of manufacturing. This makes testing your new product idea seem impossible before committing to a large investment.
Silicone casting for prototypes or small runs can be inexpensive, as the molds are often made from silicone itself and cost just a few hundred dollars. However, industrial-scale production molding, which uses steel molds for thousands of parts, represents a much larger initial investment.

It's important to distinguish between "casting" and "production molding." When people talk about inexpensive silicone casting, they are usually referring to making a small number of parts using a soft mold made from RTV (Room Temperature Vulcanizing) silicone. This is a fantastic method for prototyping. We can create a master model, often 3D printed, and then create a flexible silicone mold from it. This is perfect for testing a design's form and function. However, these soft molds wear out quickly and are not suitable for mass production. For that, we need to switch to production molding, which uses robust steel molds. While the initial investment is higher, the cost per piece becomes very low at high volumes, and the quality is perfectly consistent every time.
Feature |
Silicone Casting (Prototyping) |
Production Molding (Mass Production) |
Mold Material |
RTV Silicone |
Hardened Steel |
Mold Cost |
$200 - $800 |
$1,500 - $10,000+ |
Mold Lifespan |
10 - 50 parts |
100,000 - 1,000,000+ parts |
Best For |
Design validation, small batches, hobbyists. |
High-volume, consistent, commercial products. |
Why are silicone molds so expensive?
You receive a quote for a production mold and get sticker shock. It just looks like a block of metal, so it's hard to understand why it costs thousands of dollars.
Production silicone molds are expensive because they are precision-machined from high-grade hardened steel. The cost reflects the complex CNC programming, skilled labor, precise engineering for features like undercuts, and the durability required to produce hundreds of thousands of perfect parts.

A production mold is a highly engineered industrial tool, and its price reflects that. The process begins with a block of high-quality P20 or S136 steel. This steel alone can be costly. Then, our engineers spend hours programming CNC (Computer Numerical Control) machines to carve out your product's design with incredible precision, often down to a fraction of a millimeter. The more complex the design—with fine textures, undercuts, or thin walls—the more machine time and specialized tooling are required. After machining, the mold is hand-polished to achieve the desired surface finish. This skilled labor adds to the cost. Finally, the mold is built to withstand immense pressure and high temperatures for hundreds of thousands of cycles without degrading. It's not just a block of metal; it's a long-term investment in consistent, high-volume quality for your product.
Cost Driver |
Description |
Impact on Price |
Material |
High-grade hardened steel is used for durability. |
Higher quality steel for longer mold life increases cost. |
Machining |
Precision CNC milling and EDM for complex shapes. |
More complex designs require more machine hours, raising the price. |
Labor |
Skilled engineers for programming and technicians for polishing. |
Hand-polishing and complex setups add to the labor cost. |
Complexity |
Features like undercuts, threads, or multiple cavities. |
Increases engineering and machining time significantly. |
Is silicone costly?
You are choosing the material for your new product. Silicone often seems pricier than common plastics or other types of rubber, making you question if it's the right financial choice.
Yes, raw silicone material is generally more costly than many plastics and other synthetic rubbers. Its price reflects its superior properties, including high heat resistance, flexibility, durability, and inherent safety (biocompatibility), which cheaper materials cannot match.
When comparing material costs, it's true that silicone often has a higher price per kilogram. But the initial cost doesn't tell the whole story. You're paying for performance. Silicone can withstand temperatures from -50°C to over 200°C, something most plastics can't handle. It's UV resistant, so it won't degrade in sunlight. It's also incredibly durable and flexible, lasting for years where other materials might crack or become brittle. Most importantly, especially for our baby and outdoor product lines, high-purity silicone is biocompatible and safe for food contact. When Alex, the procurement manager, is sourcing for a premium baby product, the safety and longevity offered by food-grade silicone justifies the higher material cost. It protects the end-user and the brand's reputation, providing value far beyond its initial price.
Material |
Relative Cost |
Key Advantage |
Key Disadvantage |
Silicone Rubber |
High |
Excellent heat resistance, safety, durability. |
Higher initial cost. |
TPE Plastic |
Medium |
Cheaper than silicone, good flexibility. |
Lower heat resistance, less durable. |
Natural Rubber |
Low-Medium |
High elasticity, inexpensive. |
Poor UV/ozone resistance, potential allergens. |
What is a cheap alternative to silicone molds?
You need a mold for a one-off project or a hobby. A professional steel mold is major overkill and far too expensive for your needs, so you need a more accessible solution.
For DIY projects or very small batches, cheap alternatives include making your own molds from RTV silicone, using urethane rubber, or even 3D printing a mold with high-temperature resin. These are not suitable for mass production but are great for prototyping.

For anyone working outside of industrial manufacturing, there are great, affordable ways to create molds. The most popular is using a two-part RTV silicone kit. You can build a box around your master part and pour the liquid silicone over it to create a flexible mold, perfect for casting a handful of copies in resin or wax. Another option gaining popularity is 3D printing. Using a high-temperature resin, you can 3D print a rigid mold directly from a CAD file. This is incredibly fast for creating a single prototype. Urethane and other hard rubbers are also used. It's crucial to remember that these are all for low-volume applications. They lack the durability and precision of a steel production mold and would fail quickly under the heat and pressure of industrial compression molding. They are a means to an end for prototyping, not an alternative for manufacturing.
Alternative Mold Type |
Best For |
Pros |
Cons |
RTV Silicone Molds |
Hobbyists, resin casting |
Flexible, captures fine details. |
Very low lifespan (10-50 uses). |
3D-Printed Molds |
Quick single prototypes |
Extremely fast to create. |
Brittle, limited material compatibility. |
Urethane Molds |
Small batch casting |
More durable than silicone molds. |
Can be rigid and difficult to de-mold. |
Does the Dollar Tree sell silicone molds?
You see extremely cheap silicone molds in discount stores. This makes you wonder if they can be used for a real product, or why a custom mold costs so much more.
Yes, stores like Dollar Tree often sell simple silicone molds for ice or baking. These are very thin, consumer-grade molds made with the cheapest possible materials and are not intended for repeated, high-temperature industrial use. They are not a substitute for durable production molds.

This is a great question because it perfectly illustrates the difference between a consumer product and an industrial tool. The silicone ice tray or baking mold you find at a discount store is designed for a very different purpose. It's made from a lower grade of silicone, often peroxide-cured and containing fillers to reduce cost. It's also very thin to save material. It only needs to survive occasional use in a home kitchen. A custom production mold, which we make at Mitour, is a heavy-duty tool. It is engineered to produce hundreds of thousands of identical parts under intense heat and pressure without warping or degrading. The difference is like comparing a toy plastic hammer to a professional-grade steel sledgehammer. While both are called "molds" and are made of "silicone," their quality, durability, and purpose are worlds apart, which is reflected in their price.
Feature |
Discount Store Mold |
Custom Production Mold |
Intended Use |
Home, occasional use. |
Industrial, mass production. |
Material Grade |
Low-cost consumer grade. |
High-purity, certified industrial grade. |
Durability |
Low; may tear or warp easily. |
Extremely high; lasts for 100,000+ cycles. |
Precision |
Low; dimensions can be inconsistent. |
High; precise to fractions of a millimeter. |
How much do custom silicone molds cost?
You're ready to start your project and need a real budget number. Vague answers and wide ranges don't help you plan, so you need to know what factors determine the final price.
A custom silicone production mold costs between $1,500 and $10,000+, while a simpler prototype mold is typically $200 to $800. The final price is determined by your product's size, the complexity of its design, and the number of cavities in the mold.

When a client sends us a 3D file for a quote, we analyze several key factors to determine the mold cost. The first is size. A larger product simply requires a larger, more expensive block of steel. The second is complexity. A simple, flat part like a coaster is much cheaper to machine than a part with deep ribs, complex curves, or undercuts that require special mold actions. The third, and very important, factor is the number of cavities. A single-cavity mold produces one part at a time. A multi-cavity mold might produce 4, 8, or even 16 parts at once. While a multi-cavity mold is more expensive to build, it dramatically lowers the per-part price, making it more efficient for high-volume orders. Providing us with a detailed 3D file is the only way to get a truly accurate quote.
Cost Factor |
Low-Cost Example |
High-Cost Example |
Product Size |
Small button or seal. |
Large baking mat or case. |
Design Complexity |
A simple, flat disc. |
A bellows with undercuts. |
Number of Cavities |
Single-cavity mold. |
16-cavity mold. |
Steel & Lifespan |
Standard P20 steel for 100k shots. |
Hardened S136 steel for 1M+ shots. |
Conclusion
The cost of silicone molding is a direct investment in your product's quality and scalability. Understanding the difference between prototyping and production tools ensures you budget effectively for a successful and professional launch.